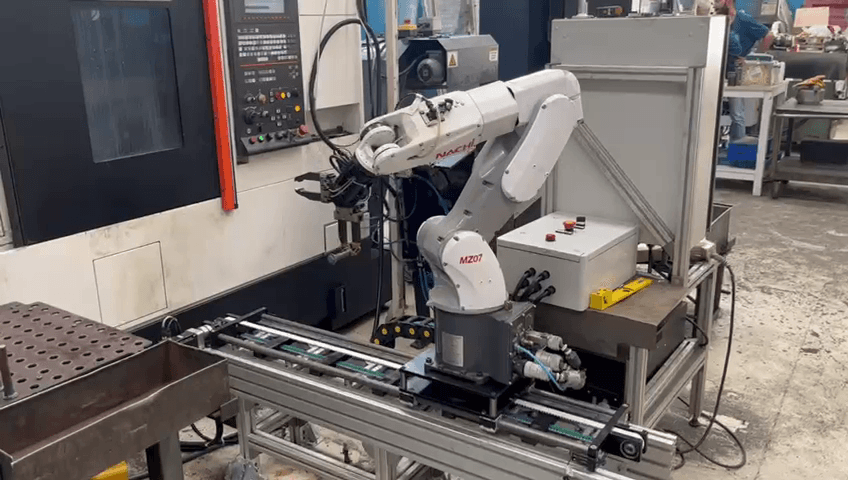
igus seventh axis expands the working space of an industrial robot
Hardware Price:
DOF
7
Max. velocity
0.3
meters per second
Repeatability
0.3
mm
Enhanced Efficiency with Up to 4x More Working Space: Automating CNC Machine Tending
Automating the loading and unloading process for CNC machines has been achieved through the integration of a NACHI robot, Schunk end effectors, and a drylin® seventh axis. This setup significantly expands the working space, allowing the robot to reach multiple zones within a single workflow. The drylin® toothed belt axes, available in three axis distances (120/160/200 mm), provide robust torque support, greater load absorption, and improved dynamics—making them ideal for industrial applications.
What is the Application?
The system automates CNC machine tending tasks, streamlining workflows through extended reach and precise handling capabilities for loading and unloading processes.
What are the Advantages of the Solution?
Extended Workspace: Up to 4x more reach for handling larger operations.
High Load Capacity: Supports radial loads up to 300 kg.
Customizable Setup: Configurable seventh axis ensures tailored integration.
What are the Advantages of the Robot?
The NACHI robot combined with drylin® axes delivers efficient functionality:
Durable Design: Lubricant-free and corrosion-resistant materials ensure longevity.
Precision Handling: Improved dynamics for smoother workflows.
Versatile Configuration: The seventh axis configurator adapts to individual applications.
Optimizing CNC Tending with Modular Linear Axes
The integration of drylin® toothed belt systems, a seventh axis, and advanced robotic components maximizes efficiency by extending workspace and improving load management. This solution exemplifies flexibility, durability, and precision in CNC machine automation, paving the way for streamlined production workflows.
0 Components