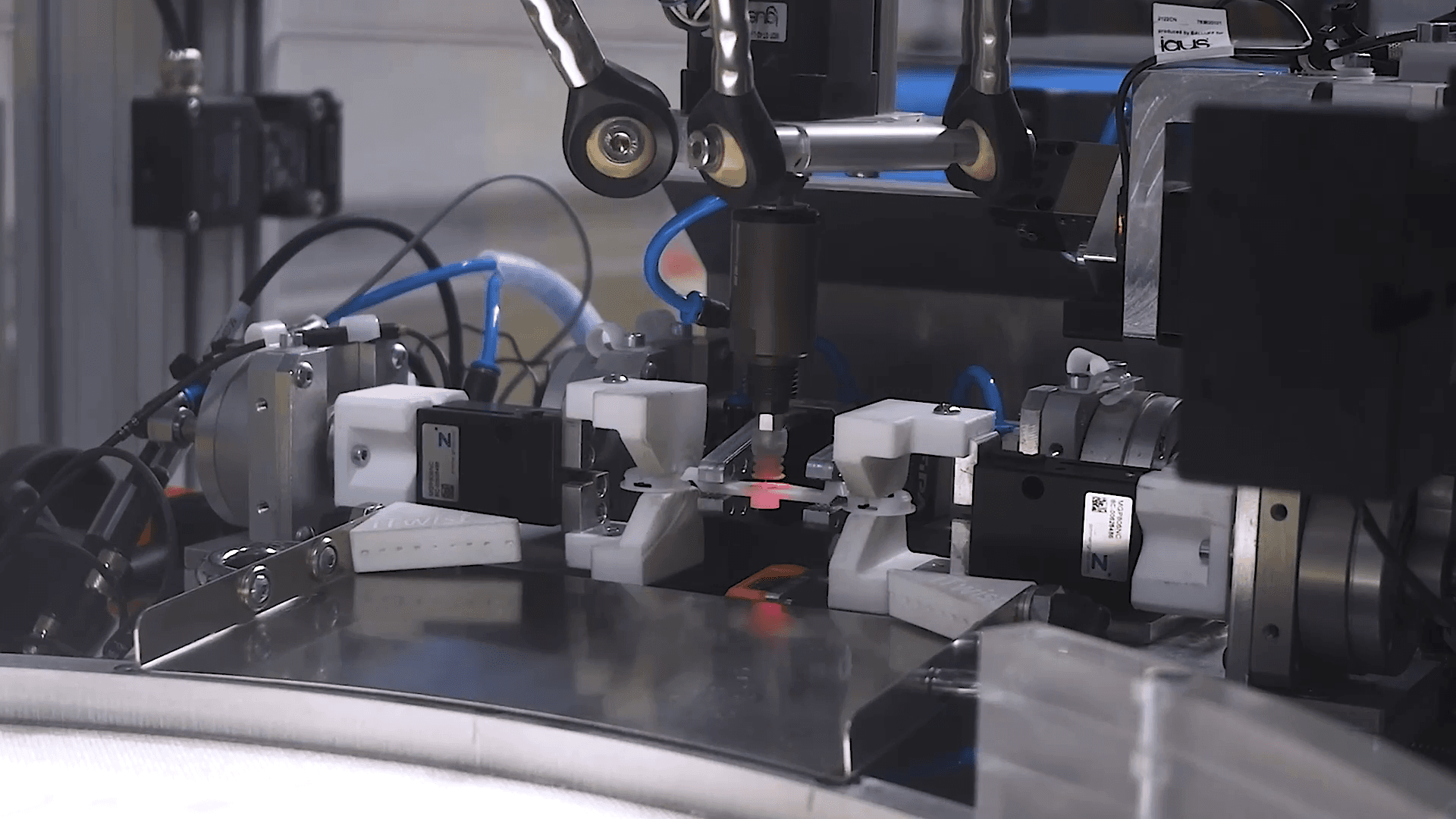
Downstream sprue separation of clip bearings
Hardware Price:
DOF
3
Repeatability
0.5
mm
Max. velocity
3
meters per second
Sprue Separation in Injection Molding with Delta Robot: Precision and Efficiency
Efficient sprue separation is a vital step in injection molding production, especially for clip bearings. This advanced solution integrates a Delta robot system, igus vacuum gripper with rotation unit, IRC, rotary conveyor, and a Zimmer gripper to automate the separation process. By combining precise detection cameras and reliable gripping technologies, the system improves speed, reduces waste, and enhances workplace safety, all while maintaining a compact footprint for easy integration.
What is the Application?
The system automates sprue separation of clip bearings post-injection molding. Using cameras to detect molding contours and grippers to handle bearings, the Delta robot ensures accurate sorting and separation.
What are the Advantages of the Solution?
Faster Production: Accelerates the separation process while maintaining accuracy.
Lower Scrap Rates: Precise handling reduces material waste.
Enhanced Safety: Automation minimizes risks associated with manual labor.
What are the Advantages of the Robot?
The Delta robot paired with specialized components offers superior performance:
Accurate Separation: Vision-guided movements ensure consistent results.
Reliable Gripping: igus and Zimmer grippers handle materials safely and efficiently.
Compact Design: Small footprint enables seamless integration into various setups.
Optimizing Injection Molding with Automated Sprue Separation
This advanced sprue separation system showcases the potential of automation in injection molding. By enhancing precision, increasing speed, and reducing waste, it paves the way for streamlined and cost-effective production workflows—an ideal solution for achieving efficiency and quality in manufacturing processes.
7 Components